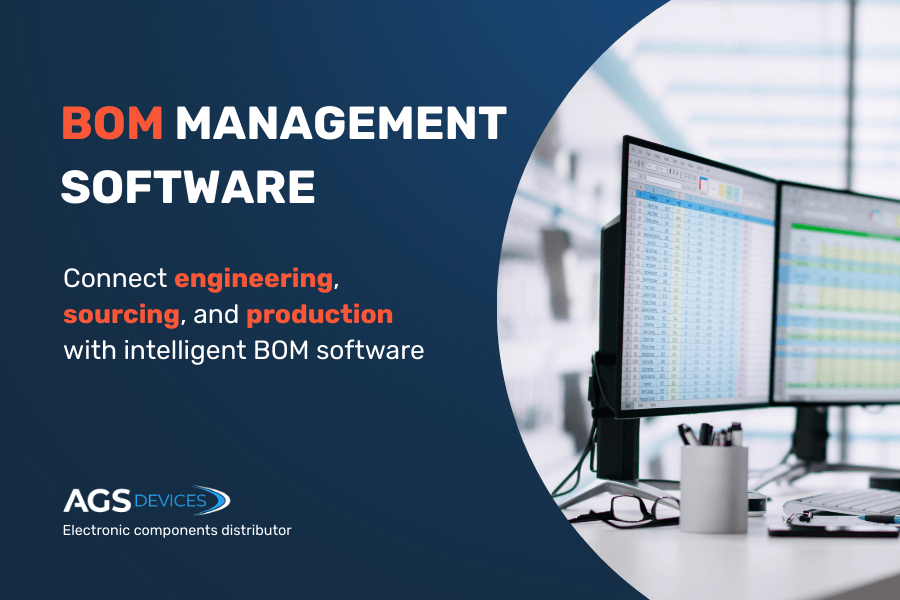
BOM Management Software: Key Points
- BOM (bill of materials) software helps manage complexity as it centralizes product data, tracks revisions, and ensures teams work from the same source of truth
- The upfront cost of BOM software can range from $50 to $300 per user/month
- 1 in 3 product launches are delayed due to inaccurate or outdated BOM data
- Choose a BOM platform that integrates with your ERP, PLM, and inventory systems to streamline data flow across teams
- Prioritize features like version control, part validation, and API access to ensure accuracy, flexibility, and long-term scalability
88% of manufacturers say better visibility in their BOM and supply chain data improves operational efficiency.
That’s because effective BOM management helps avoid costly mistakes, speeds up production, and offers a competitive edge.
This guide breaks down:
- The key features your BOM software should include
- How to evaluate platforms for scalability and accuracy
- What to consider when integrating with existing systems
- Total cost, customization, and vendor support factors
Why BOM Software Matters for Modern Manufacturing
BOM management software helps teams build, track, and update bills of materials with greater accuracy and control.
BOM software is also beneficial because:
- It improves accuracy across your product lifecycle: By consolidating component data, revision history, and sourcing info, teams can minimize manual entry errors and make sure everyone is working from the same source of truth.
- Collaboration becomes faster and easier: Real-time updates let engineers, buyers, and operations teams work together without delays, which improves time-to-market and reduces costly miscommunications.
- It supports scalability and change management: Whether you’re managing a handful of products or thousands of SKUs, the right platform should handle complex multi-level BOMs and adapt as your product line grows.
- Your supply chain becomes more agile: The right BOM tool enables smarter sourcing decisions, helps you react quickly to part shortages or EOL notices, and provides visibility into supplier options and lead times.
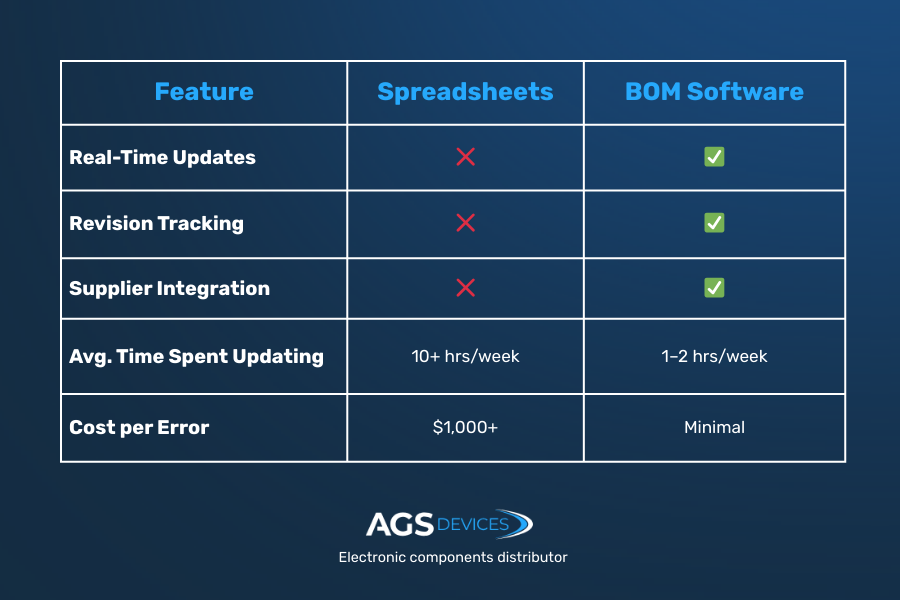
How To Choose Right BOM Management Tools in 5 Steps
Choosing BOM management software tools isn’t just about features, it’s about fit.
Here’s what to look for:
1. Match the Tool To Your Product Complexity
If you’re managing modular products, multi-level assemblies, or thousands of SKUs, choose a platform with subassembly support and part reusability.
A robotics company avoided redundant part sourcing by using software with multi-level BOM visibility.
2. Check Integration Capabilities
Your BOM system should sync seamlessly with ERP, PLM, MRP, and inventory tools to reduce manual entry and data errors.
An OEM reduced change request delays by 80% after integrating BOM software with their PLM.
3. Look for Lifecycle and Sourcing Insights:
Proactive tools flag end-of-life parts, suggest cross-references, and even pull pricing from supplier databases.
This helps you avoid redesigning or line stoppages due to obsolete components.
4. Evaluate Collaboration and Access Controls
Real-time updates, role-based permissions, and audit trails are crucial for multi-site teams.
Cloud-based tools make it easier to collaborate across engineering, procurement, and manufacturing.
5. Consider Onboarding, Support, and Vendor Reputation
Great features mean little if adoption is poor. Choose a platform that offers hands-on onboarding, training sessions, and responsive vendor support.
Bill of Material Software Core Features
The best BOM management software isn’t just a digital spreadsheet. It’s a connected, intelligent system that helps teams manage complexity, reduce risk, and scale production.
Here are the core features you should have in mind when choosing BOM management software.
1. Real-Time Collaboration and Multi-Level BOM Support
Modern product development is rarely a solo effort. Look for platforms that enable real-time collaboration across engineering, procurement, and production teams.
Multi-level BOM support allows you to break down complex assemblies into subassemblies for better visibility and control.
Pro tip: Choose BOM software that offers comment threads and activity logs on each component. It keeps decision-making transparent across your teams.
2. Integration With ERP, PLM, and Inventory Systems
BOM software should fit into your existing ecosystem. Native or API-based integration with ERP (Enterprise Resource Planning), PLM (Product Lifecycle Management), and inventory systems ensures that product data stays consistent across departments.
Pro tip: Make sure your BOM platform supports RESTful APIs as it’ll save you time and cost down the line when expanding your digital stack.
3. Version Control and Change Tracking
A single change in your BOM can ripple across procurement and production.
Robust version control ensures you’re always working on the most up-to-date iteration, while change tracking gives stakeholders visibility into who changed what, when, and why.
Pro tip: Look for tools that allow side-by-side BOM comparisons — they’re useful when reviewing revisions or explaining changes to non-technical stakeholders.
4. Component Lifecycle and Obsolescence Management
Parts don’t last forever. Your BOM tool should flag lifecycle risks, track end-of-life (EOL) notices, and suggest alternatives before a shortage hits. This proactive approach helps you avoid delays and design disruptions, especially important when dealing with long lead times or constrained supply chains.
Pro tip: Choose platforms that link to real-time databases like SiliconExpert or Octopart for automatic lifecycle updates and replacement suggestions.
BOM Software Cost, Customization, and Vendor Support
Evaluating BOM management software goes beyond feature lists, it’s about total operational impact.
Here’s how to make a more strategic and numbers-backed decision:
Total Cost of Ownership and ROI
The upfront cost of BOM software can range from $50 to $300 per user/month, but the real savings come from avoided inefficiencies:
- Manual BOM errors cost companies an average of $10,000–$50,000 per product launch due to sourcing delays and rework
- Platforms with real-time cost tracking and supplier integration can reduce sourcing time by up to 40%.
- Avoiding just one major component mismatch or obsolescence issue — which can delay production by 3–6 weeks — can save $100K+ in revenue for mid-sized manufacturers.
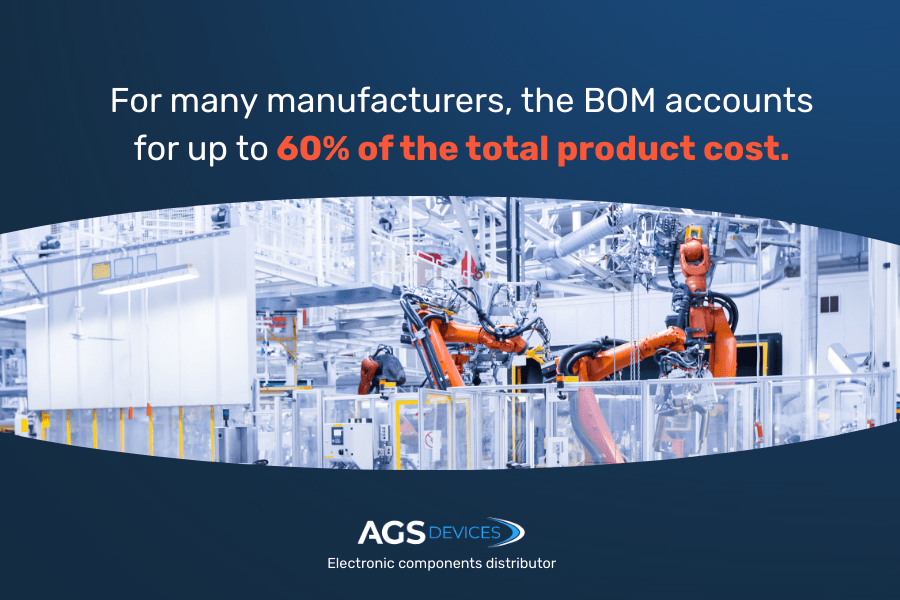
Customization and API Access for Engineering Teams
Not all BOM workflows are created equal, and rigid platforms cost more in the long run.
- Ensure the tool offers RESTful APIs and support
- Platforms like Arena PLM or OpenBOM allow custom fields, multi-currency support, and engineering change request (ECR) integration — all crucial if you manage multiple suppliers or global teams.
- If your team writes custom scripts to pull component prices from DigiKey or Octopart, API access is non-negotiable.
Onboarding, Training, and Long-Term Vendor Support
A steep learning curve can kill adoption.
Ask these support-specific questions:
- How fast can your team get onboarded? The average onboarding time for flexible platforms is 2–4 weeks, versus 2–3 months for legacy ERP solutions.
- Do they offer onboarding credits or live support? Top vendors provide on-demand training, live chat, and dedicated customer success managers.
- What’s the SLA for support? Look for guaranteed response times within 24 hours, and resolution within 72 hours for critical issues.
Evaluating BOM Software for Accuracy and Scalability
Not all BOM platforms are equipped to handle growth. As products become more complex and operations span multiple locations, your software needs to maintain accuracy at scale — without slowing your team down.
1. Scalability for Complex and Growing Product Lines
When managing high-mix product lines or fast-paced design iterations, scalability is non-negotiable. BOM software should support configurable assemblies, large part libraries, and multi-level hierarchies.
Example: A modular robotics manufacturer managing over 1,000 components across 200+ SKUs used scalable BOM tools to centralize subassemblies and reuse data across multiple products.
2. Data Accuracy and Error Reduction Features
Accurate BOMs are critical for procurement, production, and compliance. Features like built-in part validation, automatic duplication checks, and supplier data syncing can drastically reduce human error.
Example: An electronics manufacturing company exporting to regulated markets relied on BOM validation tools to ensure RoHS-compliant part selection and avoid costly product recalls due to incorrect material declarations.
3. Support for Multi-Site and Global Teams
Global collaboration requires systems that allow version access across time zones and languages. Look for role-based permissions, audit trails, and platform-wide search to keep everyone aligned.
Example: A medtech supplier with engineering teams in the U.S. and Europe used a cloud-based BOM system to synchronize documentation in real time, allowing for faster approval cycles and smoother compliance across regions.
4. Cloud-Based vs. On-Premise Solutions
Each deployment model has its pros and cons. Cloud platforms are easier to maintain, ideal for distributed teams, and often more scalable. On-premise options offer more control, which is sometimes preferred in aerospace or defense settings.
Example: A semiconductor manufacturing company developing critical components for defense programs opted for an on-premise BOM tool with secure VPN access, while their consumer electronics division used a cloud-based platform to accelerate product releases.
BOM Management Software: Key Takeaways
- Modern BOM management software isn’t optional since it’s a foundational tool for scaling production and avoiding costly errors.
- Integration and data accuracy are essential when evaluating solutions for engineering and supply chain teams.
- Customization and vendor support impact your long-term ROI — from onboarding to software scalability.
- The best tools flag obsolescence and component risk early, allowing you to plan alternatives and stay ahead of shortages.
Why Manufacturers Choose AGS Devices for BOM Optimization
Your BOM management software should be a strategic asset, not a bottleneck. At AGS Devices, we go beyond basic tools by offering end-to-end BOM management solutions backed by sourcing expertise and real-time data insights.
Our platform enables fast, scalable BOM processing, complete with automated validation, component cross-referencing, and lifecycle risk analysis.
In addition to robust BOM support, we provide:
Whether you’re scaling production, managing multi-site teams, or optimizing complex assemblies, AGS Devices helps you maintain accuracy, reduce costs, and respond quickly to component challenges.