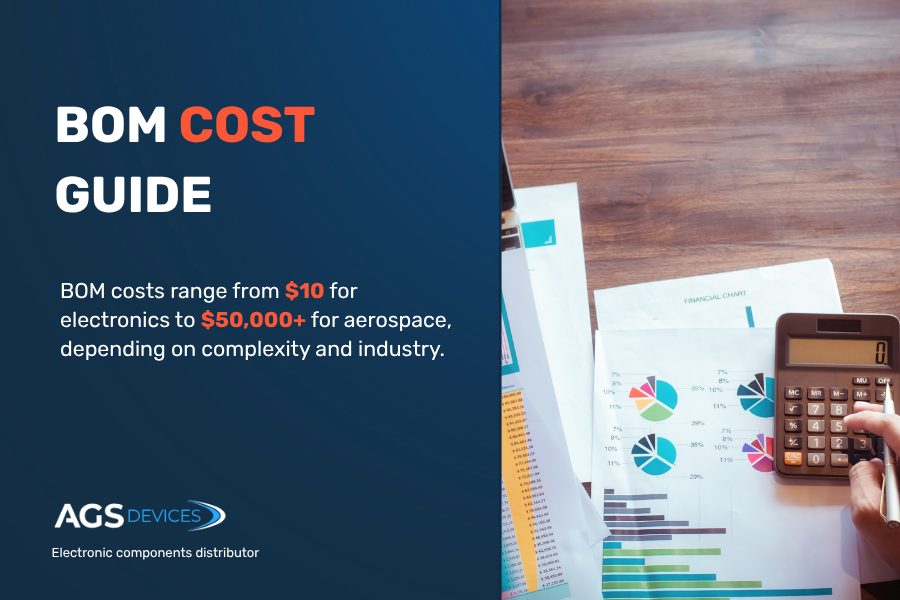
BOM Cost: Key Takeaways
- BOM cost can account for up to 70% of total product manufacturing expenses
- Poor sourcing decisions raise BOM costs by 15–25% due to shortages, EOL parts, and lack of visibility
- Cross-referenced alternates and part consolidation are proven strategies for fast cost reduction
- Lifecycle-aware sourcing prevents costly redesigns and production delays
- Digital BOM management software tools improve accuracy, track pricing, and flag obsolescence risks in real time
- Global supplier diversification helps minimize pricing volatility and lead time risk
More than 50–70% of a product’s manufacturing cost is locked in the BOM stage.
That means every component choice, from ICs to connectors, directly affects profitability, production timelines, and supply chain resilience.
For engineers, sourcing specialists, and operations leads, understanding how to control BOM cost isn’t just helpful; it’s critical to staying competitive in a volatile market.
In this guide, we’ll break down:
- What BOM cost includes and how it’s calculated
- Common factors that drive BOM prices up
- Proven strategies to reduce BOM costs without compromising quality
- How smarter sourcing and lifecycle visibility can futureproof your production
BOM Cost in Manufacturing
BOM costs typically range from $10–$50 for consumer electronics, $100–$500 for industrial devices, and up to $50,000 or more for complex aerospace systems.
Here’s a typical cost breakdown by industry:
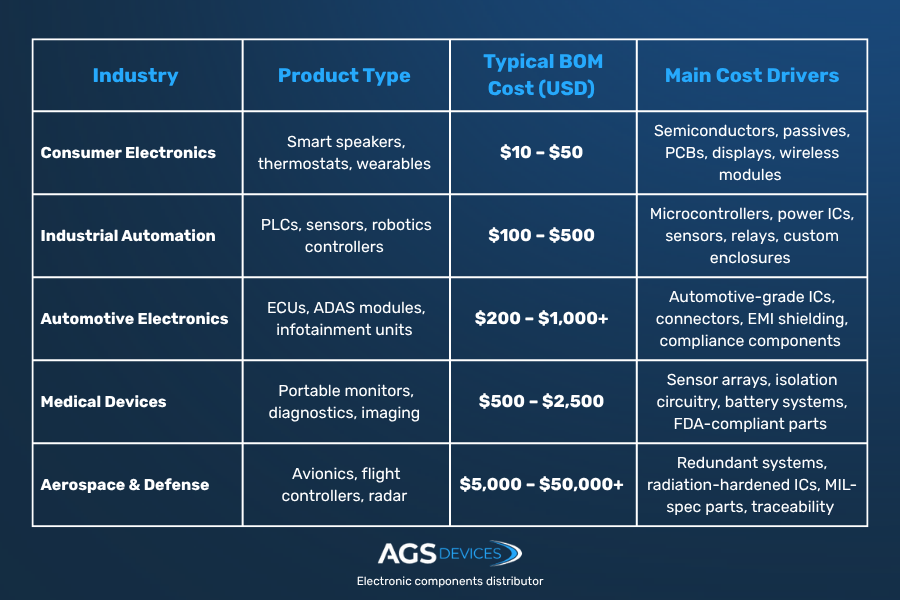
What Does BOM Cost Include?
BOM cost refers to the total cost of all components and materials required to assemble a finished product.
It includes:
- Direct materials: Resistors, capacitors, ICs, connectors, PCBs
- Subassemblies: Pre-assembled modules or systems
- Packaging and labeling: Any items required for shipping or presentation
- Procurement overhead: Freight, import tariffs, handling costs
- Tooling or one-time setup costs: For custom or specialty items
When calculating BOM costs, it’s important to distinguish between different types of BOMs such as EBOM vs MBOM.
EBOMs capture the design intent, while MBOMs reflect how a product is built, including packaging and factory-specific components.
Why BOM Cost Matters
Accurate BOM costing ensures:
- Competitive pricing: Overestimating BOM costs inflates prices
- Effective procurement: Knowing exact BOM values enables better sourcing negotiations
- Risk mitigation: Components with unstable pricing or short lifecycles can disrupt production if not tracked properly
- Scalability: Predictable BOM costs allow for smoother forecasting and budget planning
Calculating and Analyzing BOM Costs
Accurate BOM cost analysis is the foundation of cost-effective production.
How To Calculate BOM Cost
At its core, BOM cost = Σ (unit cost × quantity) for every component in the assembly.
But real-world BOM analysis requires going deeper.
Direct cost components include:
- Component unit price: Based on supplier quote or contract
- Quantity per build: Number of units required per product
- Packaging and shipping: Cost to deliver parts to the factory
- Import duties and tariffs: Especially for international sourcing
Indirect factors to include:
- Procurement overhead: Buyer labor, compliance checks, documentation
- Volume pricing tiers: Cost fluctuations based on order quantity
- Buffer stock: Extra parts added to account for defects or demand spikes
For example, let’s take a smart thermostat and assume the following component breakdown:
- Microcontroller: $3.20 × 1 = $3.20
- Temperature sensor: $1.10 × 2 = $2.20
- Wi-Fi module: $4.75 × 1 = $4.75
- Display screen: $6.00 × 1 = $6.00
- Housing plastic: $1.50 × 1 = $1.50
- PCB board: $2.25 × 1 = $2.25
Subtotal (direct costs): $19.90
Then factor in indirect costs which include:
- Shipping & tariffs: $1.25
- Procurement overhead: $0.85
Total BOM Cost = $22.00 per unit
Tip: Use lifecycle-aware pricing. Parts nearing end-of-life often cost more and create long-term risk.
Factors That Impact BOM Pricing
BOM pricing isn’t just about what a component costs on paper; it’s shaped by a wide range of dynamic variables that can fluctuate based on market, lifecycle stage, and even geopolitical conditions.
1. Component Lifecycle Status
Component lifecycle stages affect both availability and cost.
These include:
- Active parts: Generally stable pricing and consistent supply
- NRND (Not Recommended for New Design): Higher cost due to limited future availability
- EOL/Obsolete parts: Often require urgent last-time buys or risky sourcing from gray markets
Insight: Obsolete parts can inflate BOM costs by up to 3–5× due to urgency, scarcity, or redesign requirements.
2. Supplier and Distributor Pricing Models
Pricing varies based on:
- MOQ (Minimum Order Quantities): Low volume buys often carry surcharges
- Tiered pricing: Unit costs drop significantly at breakpoints (e.g., 1,000+, 10,000+ units)
- Contract terms: Annual volume agreements or preferred supplier status can reduce cost
Pro tip: Always request tiered quotes across multiple volume levels to uncover cost inflection points.
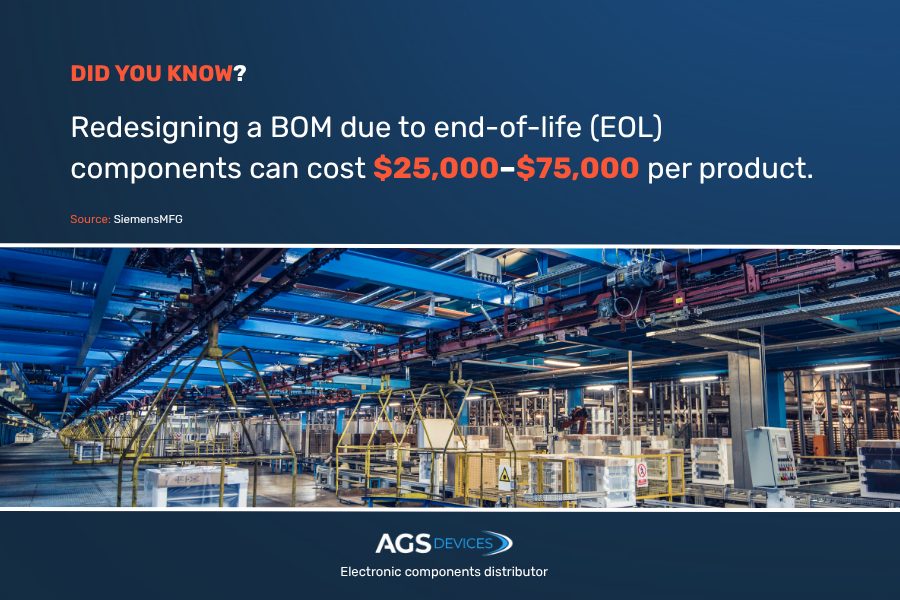
3. Lead Times and Allocation Pressures
Market dynamics and supply chain stress can force high-cost sourcing decisions.
The cost-related pressures include:
- Extended lead times can force buyers into spot buys, often at a premium
- Market shortages (e.g., semiconductors during COVID) lead to inflated pricing and long backorders
- Allocation scenarios: When demand exceeds supply, even high-volume buyers may pay more or face delays
4. Tariffs, Taxes, and Import Fees
International sourcing may involve 5–25% cost uplifts due to:
- Section 301 tariffs (U.S.–China)
- Customs duties by region
- Shipping surcharges during high-demand periods
Example: Sourcing a $1 capacitor from China could cost $1.15–$1.25 after logistics and import taxes.
5. Design Overengineering or Underspecification
Engineering decisions play a major role in BOM cost outcomes.
Design pitfalls that affect cost include:
- Overengineering: Using mil-spec or industrial-grade parts where commercial-grade would suffice
- Underspecification: Leads to part failure, warranty costs, and expensive field repairs
Balancing function, reliability, and cost is key, especially in applications like consumer electronics vs. aerospace.
6. Market Volatility and Global Events
Unpredictable global events often impact pricing and availability.
Common volatility triggers include:
- Raw material shortages (e.g., rare earths, neon gas) impact prices globally
- Geopolitical tensions (e.g., U.S.–China tech restrictions) disrupt sourcing channels
- Natural disasters (e.g., fab fires, floods) reduce supply and drive up costs
Did you know: The 2021 Renesas fab fire significantly disrupted automotive chip production, contributing to increased BOM costs and production delays across the automotive sector.
4 Strategies for Reducing BOM Costs
The most effective companies embed cost-saving tactics into every phase of the product lifecycle, from component selection to vendor negotiation.
1. Standardize and Consolidate Components
Simplifying your part catalog is one of the fastest ways to reduce BOM cost and complexity.
- Use the same parts across multiple products or assemblies
- Eliminate redundant or rarely used SKUs
- Reduce the complexity of managing low-volume, unique components
Benefit: Higher order volumes on fewer parts = better pricing and reduced inventory overhead
2. Design for Sourcing (DFS)
Involving procurement early helps engineering teams make cost-conscious choices from the start.
- Involve procurement teams during the design phase
- Avoid selecting hard-to-source or EOL components
- Choose footprint-compatible alternates to allow vendor flexibility
Example: Replacing a custom connector with a pin-compatible standard version can significantly reduce BOM cost and tooling complexity
3. Use Cross-References and Alternate Parts
Maintain approved alternates in your BOM for critical components
Leverage cross-referencing tools to find functional equivalents with better pricing or shorter lead times
Tools to use:
- Octopart
- SiliconExpert
- Manufacturer cross-reference databases
Tip: Ensure alternates meet voltage, tolerance, and package specs; don’t trade savings for compliance risk.
4. Negotiate Tiered and Contract Pricing
Pricing leverage improves when you consolidate demand and plan ahead.
- Secure volume-based discounts through planned purchase commitments
- Bundle BOMs across SKUs when possible to gain price leverage
Pro tip: Partner with authorized distributors who can negotiate tiered pricing on your behalf and offer better visibility on supply trends.
How AGS Devices Supports Costed BOMs
Your BOM isn’t just a list of parts. It’s the single greatest lever for controlling manufacturing cost, accelerating production, and safeguarding your supply chain.
When optimized, a costed BOM aligns engineering, sourcing, and operations, preventing overruns, avoiding redesigns, and unlocking scalable efficiency.
At AGS Devices, we help manufacturers reduce BOM costs through:
Whether you’re launching a new product or refining a legacy BOM, we bring the tools, global supplier access, and technical expertise to keep your costs low, and your operations moving.
BOM Cost: FAQs
What is BOM cost?
BOM cost refers to the total expense of all materials and components listed in a product’s bill of materials (BOM).
How do you calculate BOM cost?
To calculate BOM cost, multiply the unit price of each component by the quantity used in the assembly:
BOM Cost = Σ (Unit Cost × Quantity per Part)
Then add indirect costs such as shipping, tariffs, and procurement overhead for a more accurate total. Tools like ERP systems and BOM management software help automate and standardize this process.
What is a costed BOM?
A costed BOM is a bill of materials that includes specific pricing for each part listed. It shows the total material cost for one unit of a product and is essential for budgeting, forecasting, and profit margin analysis. A costed BOM is typically updated in real time using supplier pricing feeds or ERP integrations.
What factors increase BOM costs?
Common reasons BOM costs rise include:
- Sourcing obsolete or EOL (end-of-life) parts
- Using over-specified components
- Not leveraging cross-referenced alternates
- Ignoring supplier MOQs and volume-based discounts
- Relying on fragmented or outdated supplier data
How can you reduce BOM costs?
You can reduce BOM cost by:
- Consolidating part numbers across designs
- Using approved alternates with better availability or pricing
- Designing for sourcing early in the product lifecycle
- Tracking component lifecycle to avoid last-time buys
- Partnering with a sourcing expert like AGS Devices for global, vetted supplier access